How to form a faucet from a brass rod? The Manufacturing Process of a Faucet?
Do you know what a Brass rod is? And how is a brass rod processed into a faucet?
A brass rod is a solid brass bar that has been extruded or drawn. There are many types of brass rods, including purple brass rods, brass rods, white brass rods and bronze rods.
Brass bar forming has its own principles. The process of forming brass rods can also be described as the production process of brass rods. Different types of brass rods have different molding processes and different characteristics.
What are the materials of brass bars?
Brass bar materials include H59, H59-1, H59-2, H59-3, H60, H60-2, H62, H63, H65, H68, H70, H80, H90; C1100, C1020, C2680, C2800, C2600, C2801, C5191, C5210, C2200, C7521 C7541, C17200, C1070, C7701, QSn6.5-0.1, QSn8-0.3, QSn4-0.3, BZn18-18, BZn15-20, CuBe2, etc.
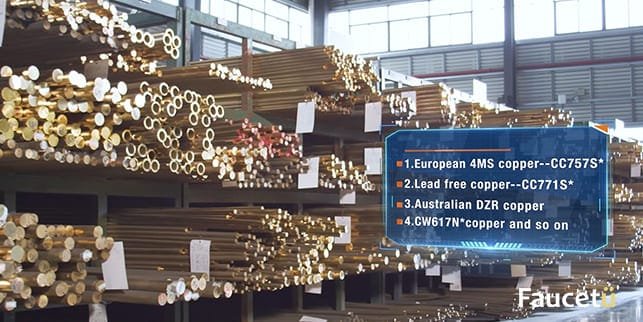
What are the brass rod forming to faucet processes?
There are many brass bar forming to faucet processes, including extrusion, rolling, continuous casting, stretching, etc.
There are three brass rod forming to faucet process flows, as follows:
1. Pressing-(rolling)-drawing-(annealing)-finishing-finished faucet.
2. Continuous Casting (up-intake, horizontal or wheeled, crawler, dipping)-(rolling)-stretching-(annealing)-finishing-finished faucet.
3. Continuous extrusion – stretching – (annealing) – finishing – finished faucet.
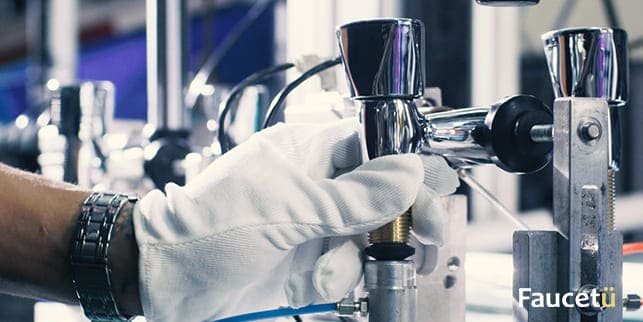
Brass bar forming to the faucet process of extrusion?
1. The type of extrusion: extrusion is divided into forward extrusion, reverse extrusion and special extrusion three.
(1) Forward extrusion: refers to the extrusion of products in the same direction as the direction of extrusion pressure extrusion behavior.
(2) Reverse extrusion: is the direction of extrusion and extrusion pressure in the opposite direction.
(3) Special extrusion: refers to other extrusion methods such as hydrostatic extrusion.
2. The characteristics of extrusion:
(1) The characteristics of forward extrusion: where the forward extrusion equipment is simpler and most widely used.
(2) The characteristics of directional extrusion: reverse extrusion due to reduce the friction between the billet and the extrusion cylinder, reducing the extrusion pressure, can improve the tool life, in small and medium-sized extruded products are used more.
(3) The characteristics of special extrusion: special extrusion is mostly used in the extrusion of special products.
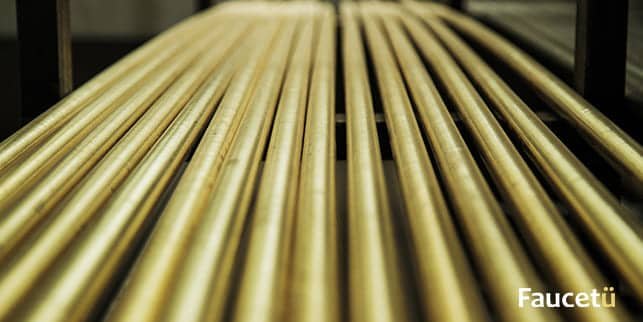
What steps are needed to process brass rods into faucets?
1. Cutting
First of all, the brass bar needs to be cut, cutting process: water gun cutting (water jet), laser cutting, wire cutting, etc.
A. Water gun cutting is water jet cutting, commonly known as the water jet. With the development of science and technology, this cold cut method will be more areas of application, belongs to a new cold processing process, it can be used in harsh conditions and strictly prohibit the use of smoke and fire site, has been widely valued, water jet cutting is a set of mechanical, electronic, computer, automatic control technology as one of the high-tech achievements, is a new material processing method developed in recent years.
The principle of water jet cutting is to use a certain high pressure of pure water or liquid slurry with cutting abrasive, through the cutting nozzle shot with the high-density impact of the liquid column, straight into the object to be processed for cutting. According to the different levels of water pressure, can be divided into low-pressure and high-pressure water jet cutting two.
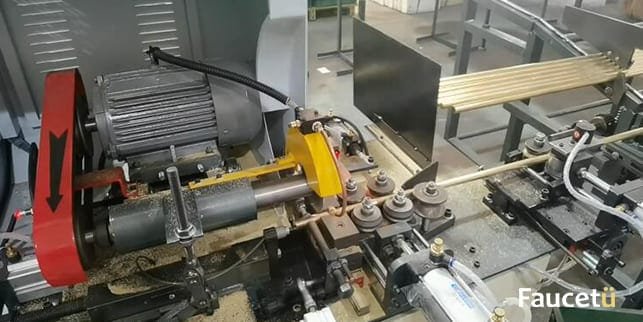
B. Laser cutting uses a high power density laser beam to irradiate the material to be cut, so that the material is quickly heated to vaporization temperature, evaporation to form holes, with the beam to the material movement, the holes continuously form a very narrow width of the slit to complete the cutting of the material.
It is the use of a focused high power density laser beam to irradiate the workpiece, so that the irradiated material quickly melts, vaporizes, ablates or reaches the ignition point, while the molten material is blown away with the help of a high-speed airflow coaxial to the beam, thus realizing the cutting of the workpiece. Laser cutting is one of the thermal cutting methods. It can be divided into four categories: laser vapor cutting, laser melting cutting, laser oxygen cutting and laser scribing with controlled fracture.
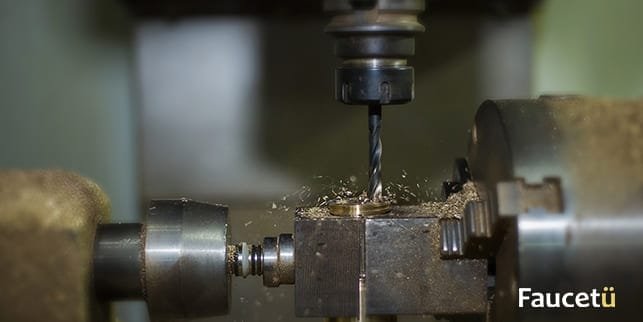
C. Wire cutting is the abbreviation for wire cutting and refers to a processing method. It is developed on the basis of EDM piercing and forming processing. It is a processing method that uses a moving metal wire (molybdenum wire, copper wire or alloy wire) as the electrode wire, and relies on the pulse electric spark discharge between the electrode wire and the workpiece to produce high temperature to melt or vaporize the metal and form a cut to cut out the part.
By cutting the copper bar to get the size we need for the production of faucets before the next step of processing.
2. Finishing
Finishing refers to the machining, in order to make the workpiece to achieve higher precision and surface quality requirements of processing. Generally after rough machining and semi-finishing machining. After the cutting copper bar is mechanically finished, it becomes each part of the faucet for the next operation.
3. Polishing
Polishing refers to the use of mechanical, chemical or electrochemical action to reduce the surface roughness of the workpiece, in order to obtain a bright, flat surface processing methods.
Is the use of polishing tools and abrasive particles or other polishing media on the surface of the workpiece finishing process. Polishing can not improve the dimensional accuracy or geometric shape accuracy of the workpiece, but to get a smooth surface or mirror gloss.
Polishing, polishing workers through the high-speed rotation of the polishing wheel pressure to the workpiece, so that the abrasive on the main surface of the faucet tumbling and micro cutting, so as to obtain a bright processing surface, when using non-grease matting polish, can be matted to improve the appearance of the bright surface. When producing faucets, we often use the roller polishing method.
4. Electroplating
After polishing, the faucet parts need to be plated with copper first to enhance the adhesion of plating, and then plated with nickel layer (including semi-gloss nickel and bright nickel) nickel layer plays a role in corrosion resistance, and because nickel itself is a soft material and dark color, so the last will be plated with a layer of chromium layer on the nickel layer to harden the surface while improving the brightness.
5. Assembling
Prepare the whole set of product assembly accessories, such as: handles, handle screws, red and blue beads, spool, pressure cap, half circle, O-ring, spout, bubbler, cotton bag, color box, outer box, etc.. Assemble into a complete set of faucet on the assembly line.
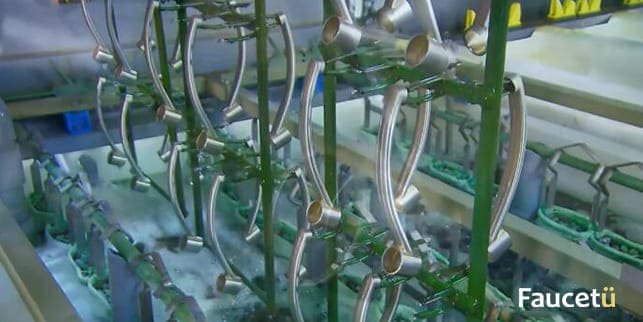
6. Inspection
After the faucet is assembled, it needs to go through a machine pressure test and water test, and after the finished product is inspected, the packaging is completed and finally shipped to consumers all over the world.
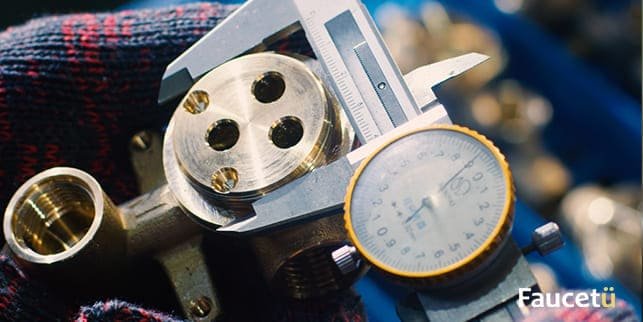
All-brass faucet is the best quality among all other materials produced faucets.
The advantages of all-copper faucets are:
- All copper faucet belongs to the non-ferrous metal, first of all, the value (seawater immersion, 100 years before corrosion 3MM).
- Faucets in the copper surface of the harmful bacteria directly kill, such as Streptococcus aureus, Salmonella, etc..
- The surface of the patina has the role of sealing, to prevent the seal failure after a long period of time.
- Easy to maintain.